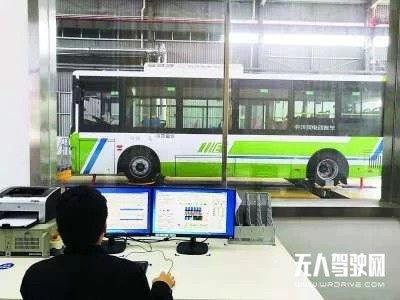
這些車輛都來自同一個地方——開沃汽車集團旗下子公司南京金龍客車制造有限公司。近日,記者走進這座省工業互聯網“標桿工廠”。
全流程數字化管控,生產效率提高20%以上
走進南京金龍制造工廠,高度智能化的生產車間里,充斥著各類機器忙碌的聲音,生產線上只有少量人員在各自崗位上。在所有生產車間中,焊裝車間的智能化率超過90%。另外,涂裝車間的涂膠、噴漆和總裝車間的大型零部件搬運等也都大量采用了機器人作業。
開沃汽車集團科技規劃部副總監王春海介紹,公司在2017年通過兩化融合管理體系評定,近幾年加大在工業互聯網建設方面的投入,建設新能源汽車制造工業互聯網工廠。
王春海說,標桿工廠的建設包括CAD、ERP、MES等系統在內的信息化系統,實現從設計、生產、采購、銷售、售后等各環節的網絡化、智能化的提升,實現運營全過程的數字化、可視化、透明化、規范化,實現全流程管控。
截至目前,標桿工廠使新能源汽車制造的生產效率提高20%以上、運營成本降低20%以上、產品研制周期縮短30%以上、產品不良品率降低20%以上、單位產值能耗降低10%以上,不僅提高了企業核心競爭力,更促進了新能源汽車行業的發展。
開發節能APP,拓展“產品+服務”提升效益
嘗到“甜頭”后,南京金龍不斷在工業互聯網領域挖掘潛力。
王春海告訴記者,借力“互聯網+”技術,南京金龍客車自主開發一款以駕駛行為與能耗分析為主的云服務產品——“開沃節能APP”。以公交集團為主要應用對象,從客戶的實際需求出發,分析能耗的影響因素,并提供一種切實可行的節能途徑。
以該公司一款6859新能源公交車為例分析,如果糾正駕駛員的駕駛習慣,并以此駕駛員的駕駛行為為參考,平均下來每輛車的百公里電耗可降低6.33kWh,按每天每輛車跑一百公里計算,每年每輛車至少能節省電2310.45kWh。
王海春表示,該款產品適應國家相關政策的要求,有利于上市后迅速搶占市場份額,推動公司業務向售后服務、維護運行等環節拓展,從單一生產銷售轉向提供“產品+服務”,形成新的利潤增長點。
據介紹,截至2020年8月1日,這款節能APP已累計完成接入車輛近3000輛。
深耕無人駕駛領域,實現小批量商業應用
目前,汽車工業與5G的關系更加緊密,5G讓汽車駕駛超越“車聯網”時代,全面賦能自動駕駛技術,尤其是讓遠程控制自動駕駛和真正的無人駕駛汽車成為可能。
南京金龍同樣看到了機遇和挑戰,借助通信技術的進步,進一步拓展工業互聯網的應用邊界。
王春海告訴記者,目前南京金龍已在廠區實現了5G覆蓋,并將5G技術應用于智能化產品及其生產測試環節,全面賦能自動駕駛技術。
南京金龍長期致力于智能網聯技術的研發,先后成功開發了L4級微循環車、礦山卡車、道路清掃車等無人駕駛產品,并實現了小批量的商業應用。
“在開發過程中,我們意識到現有的技術條件,要實現完全意義的無人駕駛,還有很長的一段路要走。在某些先定環境下,99%的時間內,車輛可完全無人駕駛。然而,剩下的1%,特別是超出系統設計運營范圍時,需要人工介入。”王春海說,基于此種需求,南京金龍開發了基于5G的遠程駕駛系統,利用5G大帶寬、低時延的特性,實現了對超遠距離車輛的監控、接管和操控。
目前,“5G+遠程駕駛系統”已在南京金龍微循環車、礦山卡車上實現批量裝配和銷售,并正在拓展更加廣闊的應用場景,如遠程檢修、火場救援、危化品現場巡檢等。